By Kenneth Wawrew
Challenges Facing Solar Glass Manufacturers
Each of the glass industries faces their own special challenges. Solar glass producers generally manufacture both textured and clear glass. Textured or prismatic glass requires very unique optics for inspection. Inspection equipment that works well for clear glass will not address textured glass properly. The solar industry has the requirement to differentiate ¡®open¡® and ¡®closed¡® bubbles. This is not a typical requirement for glass processors. The quality of the glass edge is important to solar panel manufacturers, as is the panel size and shape.
The solar glass processors, factories that cut, grind and temper also face new challenges to ensure the end product meets the specifications of the customer. Defects in the glass come from a number of sources: defects that were not detected at the float when the glass was produced; defects produced from transporting the glass to different factories; defects produced from the processing equipment; and the logistics of handling and reworking defective glass panels. Some glass has special features such as drilled holes or special shapes such as a corner cut. Another challenge is to be able to accurately measure the size and also the shape (for example square) of the panel.
Solutions to Improved Quality
SynergX has been providing advanced automated optical inspection technology to the glass industry for over a decade. Working in partnership with many of the largest glass manufacturers, the company has provided camera-based systems to improve quality and optimize glass production processes. The company has developed systems to inspect and to provide precision measurement for textured and clear solar glass, both on the float as it is being produced and in process during the cutting and tempering steps.
For the solar glass manufacturer, ¡®Product Quality¡® is key to being competitive. Just as the standard for normal float glass manufacturing is to use Automated Optical Inspection (AOI) systems to ensure the quality of float glass, the solar glass manufacturer is now finding it is a necessity to implement AOI systems to guarantee product quality. AOI systems are used not only for product quality, but are integrated into the cutting machine to optimize cutting of the glass into panels. Solar panels generally come with a 25-year guarantee and the liability for such a guarantee can extend to component suppliers such as the glass manufacturer, not to just the panel manufacturer. Therefore, the quality of the glass panels produced becomes of utmost importance. Solar Glass is different in nature from standard glass--textured on one side, and the defects on solar glass have different priority than those of float glass. Therefore, the techniques used for standard clear float glass do not work well for textured solar glass.
Due to the specific nature of the defects to be detected in textured solar glass panels, surface scanning requires a combination of ¡®Bright Field¡® optics and ¡®Dark Field¡® optics to be able to detect and classify all of the defects required to meet the typical industry specification. For example, the information provided by both the Bright Field and Dark Field channels is required to differentiate between ¡®Open¡® and ¡®Closed¡® bubbles. ¡®Black Stones¡® can only be detected with information from the Bright Field channel.
These systems typically use line scan cameras and the Bright Field channel works on the principal of a defect in the glass obstructing light and therefore reducing the intensity of the light at that point in the scan line. The best results for solar glass are achieved using incoherent diffused LED illumination which is passed through the glass toward the line scan camera. When a defect in the glass blocks the light, there is an intensity drop on the CCD of the camera and a defect is flagged.
The Dark Field channel also employs incoherent LED illumination. In this case, a collimating lens is used to direct the light such that the light that is passed through a defect-free panel does not reach the camera. But, all areas in the field of view of the camera are illuminated from various directions, making the system insensitive to defect orientation. When a defect is encountered on the glass panel, the defect causes the light to be scattered from its normal path, thus reaching the camera and illuminating the CCD array. This condition will cause a positive spike on the scan line and will be flagged as a defect.
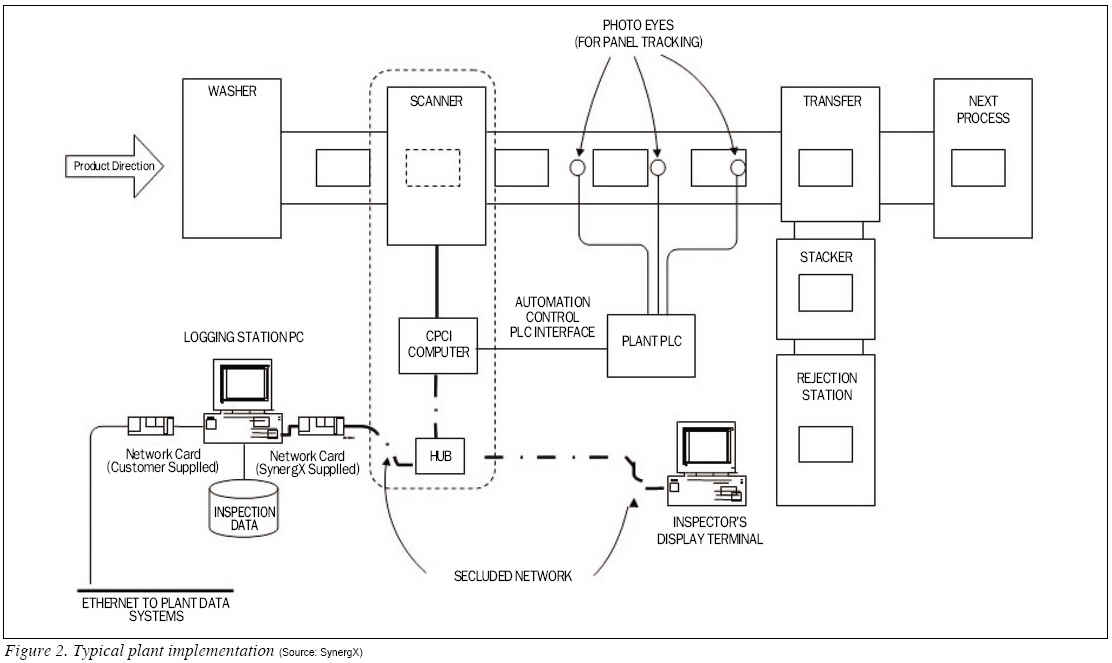
Inspection Process
Typically, the first inspection point for a glass processor would be after cutting and grinding. At this point, there is the opportunity to inspect for all surface defects such as bubbles, stones, as well as inspection of the edge of the glass for grinding defects. The size of the glass can also be measured at this point and if holes have been drilled, they can also be measured for size and position. Once other value added processes such as tempering or coatings have been applied to the glass, another inspection can be performed before shipping to the customer to ensure that there are no defects. This can facilitate automatic packing. The same issues for textured solar float glass are present with the inspection of cut or processed glass. Special techniques for textured glass have to be employed. If clear glass is processed on the same line, then switchable optics are required when processing clear glass.
Figure 2 shows a typical processed solar glass plant installation. The system is installed in process after cutting and grinding. The glass is typically washed and dried before it is inspected. By paying attention to the quality of the installation, system performance can be maximized. This means the washer and dryer should be working well producing clean and dry glass. In the plant layout diagram, there is a dotted line around the scanner. This denotes that the scanner should be maintained in a clean environment with positive air pressure fed into the scanner to minimize the opportunity of dust and foreign particles making their way onto the glass and causing a false reject. The use of a reject stacker is very important to maintain the productivity of the production line. By accumulating rejected glass in a stacker or accumulator without stopping the line, the rejected glass can then be reviewed off line not impacting the rest of the production on the line. A decision can then be made to determine if the glass can be reworked or if contamination caused the reject. The glass can be rejected at this point. An ¡®Inspector¡®s Display Terminal¡® is provided to show each panel that has been rejected and the location of all defects detected on the panel are displayed using a browser. Figure 2 also shows network connections that connect to plant data systems for analysis of the production data and also provides for a remote connection for system support and trouble shooting.
Figure 3 shows a drawing of an inspection system with the covers off, that would typically installed after cutting and grinding. A piece of the line conveyor is removed and the system is put in its place. This is a specialized transport conveyor that not only transports the glass, but provides for the laser beams that are used for edge inspection. In order to inspect the ground edge of the glass panel, the four towers shown, one at each corner of the system carry the optics for edge inspection. These towers are used to adjust the mirror carriage and keep the laser beams in focus. There is also a camera in the front of the system, the squaring camera which tells the edge inspection modules the precise positioning of the glass to be inspected. This system works on the principal of reflected light hitting the camera when a defect is detected or the absence of reflected light in normal conditions. Coherent laser illumination is used and the correct power is critical for proper detection of defects such as shiners (unground areas).
There are a number of considerations when configuring an AOI system. Typically, bright field configurations tend to work better in an industrial environment than dark field. Bright field provides much more information about the defect which allows for better classification. Bright field with collimated illumination is used for clear solar glass inspection. Bright field with diffused illumination and dark field are used for textured solar glass applications. Switchable optics to handle both clear and textured glass are required if both are to be produced on same production line.
Typical specifications for solar glass inspection applications provide for detection limits of 0.4 mm. For a clear solar glass application, AOI systems can detect and most importantly, classify a variety of defects including float glass defects and process generated defects. Examples of these defects include, bubbles, stones, scratches, edge chips, shiners produced by poor edge grinding, missing holes, chips on holes, etc. The heart of the AOI system is the ¡®Classifier¡®, the systems ability to differentiate the various types of defects and to size them accurately and consistently. Additional requirements for an AOI system may include hole inspection and special features such as a corner cut, which is quite common for clear solar glass.
In addition, AOI systems for processed solar glass should be able to track which grinder actually produced the piece of glass or in some cases which robot fed the glass to the production line. In the case of solar glass processing lines, it may be required to process both clear glass and textured glass on the same production line. In this case, selectable optics will be required to match the type of glass being processed. Textured glass requires a combination of bright field using diffused light and dark field. Clear glass requires bright filed using collimated light. Therefore, the light intensity will be automatically adjusted to match the type of the glass being processed.
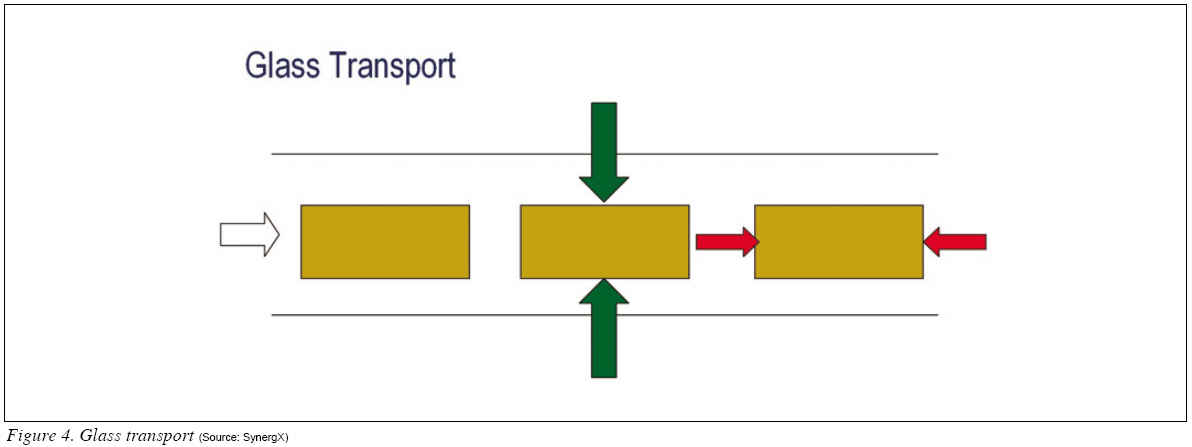
Solutions to Precision Measurement
Precision measurement and shape of glass panels are also of major concern to solar glass processors. There are two major issues that need to be considered when implementing a precision measurement system. The first being the stability of the glass transport system (the conveyor) and secondly, the imaging angles of the image of the glass panel also affect proper sizing. With most standard conveying systems, using line scan cameras, it is easy to achieve an accurate measurement of the glass panel at right angles to the conveyor, but after conducting many experiments, SynergX has found that the measurement running parallel to the conveyor is not reliable with this method.
Therefore, if accurate glass measurement and shape are important, the use of an area scan camera as opposed to a line scan camera for this function is required. If the glass panels are large, several channels or cameras can be used and the image can be stitched together. Since directional illumination is used for measurement, telecentric imaging assures that the measurement is taken from the correct spot and there are no compensation algorithms required which are typically a source of error. Through the use of these techniques it is possible to achieve measurement accuracies of ¡¾0.1 mm.
Benefits of AOI
The deployment of AOI technology in the solar glass manufacturing processes provides a number of benefits:
Human inspection is still used extensively in glass factories despite the proven inconsistency and cost of human inspectors. By applying automated optical inspection where human inspectors are used, the factory can improve its productivity and therefore, reduce the cost of manufacturing.
¡®Yield Management¡® is another major benefit of deploying AOI systems. By deploying vision systems early in the process either at the beginning of the line or after cutting and grinding, the yield of the production line can be increased substantially by not processing defective material through key value added stations such as tempering and, ultimately as this glass is used to produce a solar panel. This improvement can be anywhere from a few percent to over 10% depending on the quality of the incoming glass.
Ultimately, the use of vision systems at the various points in the production process results in a reduction in end of line defects (PPM) and it is the only method to assure consistent and reliable control on the quality of the final product.
When all these benefits are considered, solar glass manufacturers can gain a significant competitive advantage with a strategy of deploying automated optical inspection systems on their production lines.
Kenneth Wawrew is the President and Chief Executive Officer of SynergX Technologies Inc (www.www.synergx.ca).
For more information, please send your e-mails to pved@infothe.com.
¨Ï2010 www.interpv.net All rights reserved.
|